Filter Press Troubleshooting
The plates of the filter press were undergoing significant warping resulting in poor filtering, bypass, and leakage. Filter press plates should not need to be regularly replaced, but they were replacing the entire set every 3-5 months for ~$12,000 each time.
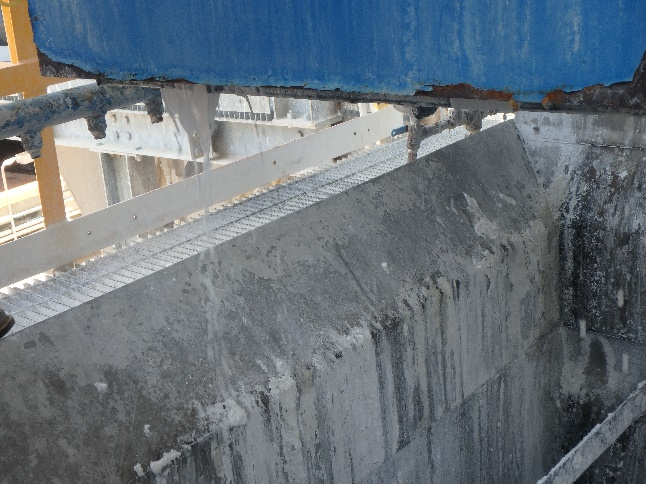
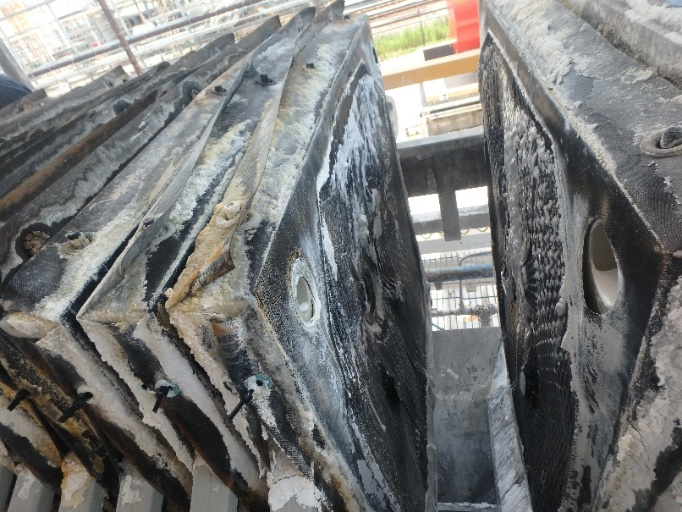
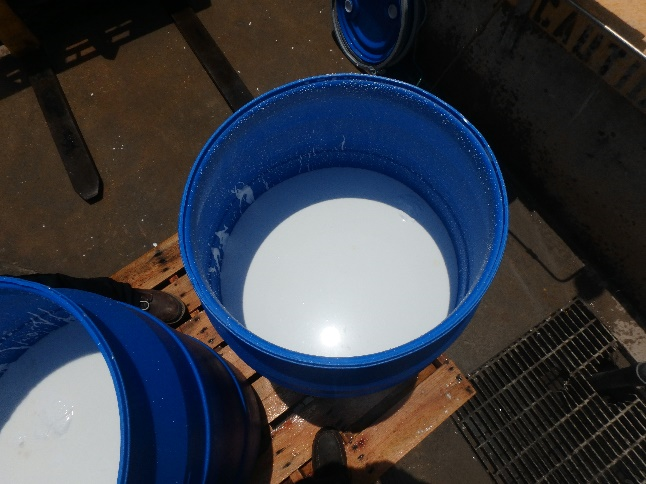
Shows leaking of the filter press and associated bowing of the plates. Consistency of cake material is also shown. All pictures were taken ~1 week before plate swap.
Examining the filter press manual thoroughly, I discovered that toluene, one of the process chemicals, was listed as chemically incompatible with the polypropylene plates. Consultation with the manufacturer indicated that the toluene in the slurry was likely chemically attacking the polypropylene plates and causing them to soften and warp; then, uneven cake buildup started occurring which accelerated the process. Fortunately, the plates could be made from alternative materials such as PVDF and Glass Filled Nylon.
My supervisor was considering purchasing one each of the PVDF and GF Nylon plates to test them out. I pointed out that the rest of the plates would still warp and then allow uneven cake buildup. As such, it wouldn’t be an accurate test of the chemical compatibility of the plates. I also noted that a chemical resistance chart showed that GF Nylon is rated slightly better than PVDF for exposure to toluene.
At the end of my internship, I wrote a 7-page memo detailing the entire process of troubleshooting the filter press. The following were the next steps that I laid out in the memo.
- Perform a more detailed economic analysis that includes labor costs.
- Scope out a capital project to purchase a complete set of GF Nylon plates.
- Establish a new protocol dictating when and how to clean the filter cloths and plates, and when to replace the cloths.
Based upon my recommendations, the company is planning to scope out a capital project to purchase a complete set of GF Nylon plates for ~$65,000 which is expected to result in annual savings of ~$27,000.